What is cavitation?
Prevent cavitation by understanding what cavitation and what causes it. EXPRO Controls published a blog post regarding an in-depth analysis of ‘what is cavitation‘ on January 29th, 2025. However, I will give a brief explanation. Cavitation is the process in which the liquid’s static pressure falls below its vapor pressure, resulting in the creation of small vapor-filled cavities in the liquid. Cavitation prevention is important because cavitation can lead to damaged equipment, loss of production efficiency, noise and vibration, and safety concerns.
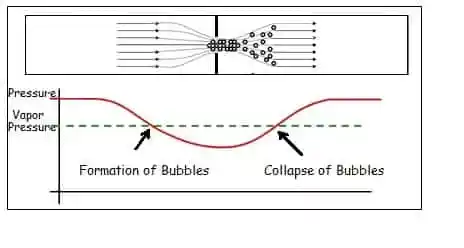
What causes cavitation?
With the knowledge of what cavitation is an understanding of what causes cavitation can be achieved. Cavitation occurs due to numerous factors, such as high fluid velocity, pressure changes, temperature, imperfect fluid flow, and surface roughness. Provided below are brief explanations for each.
- High Fluid Velocity
- When a fluid flows too quickly over a surface, such as in a pump or propeller, the pressure can drop significantly in certain areas. Thus, leading to cavitation problems.
- Pressure Changes
- If there is a sudden drop in pressure, such as in pumps, valves, or pipes, it can cause the liquid to vaporize locally. Thus, causing cavitation bubbles to form.
- Temperature
- Higher temperatures decrease the vapor pressure of the liquid, which make it easier for cavitation to occur at lower pressures.
- Imperfect Fluid Flow
- Irregular flow patterns, like turbulence or vortex formation, can cause localized low-pressure regions where cavitation can develop.
- Surface Roughness
- Rough surfaces can cause localized pressure drops, creating areas where cavitation bubbles can form and collapse.
How do I prevent cavitation?
Prevent cavitation by ensuring the root causes that create it are prevented. A few prevention measures include maintaining proper operating conditions, having the correct design for the application, increasing the system pressure, controlling flow rates, and monitoring the equipment closely. Provided below are brief explanations on each preventive measure.
- Maintaining Proper Operating Conditions
- Avoid low pressure by ensuring the pressure in critical areas remains above the vapor pressure of the liquid.
- Control the fluid temperature to keep it within a range that prevents vaporization. This can be achieved by cooling the fluid or using temperature control systems.
- Correct Designs
- Smooth flow paths for the liquid or gas reduce turbulence and sudden pressure drops. Thus, preventing the formation of vortices.
- Optimize a pump or impeller design to operate efficiently at the desired flow rates.
- Larger inlets increase the inlet diameter of the pump and can help maintain higher inlet pressure leading to a reduction in the risk of cavitation.
- Increase System Pressure
- Boosting the suction pressure at the pump inlet can lead to a reduction of cavitation. Also, by increasing the suction pressure, the system’s pressure is raised above the vapor pressure of the liquid.
- A booster pump can be installed to ensure that sufficient pressure is maintained, especially when pumping liquids at low pressures.
- Control Flow Rates
- By adjusting flow rates to flow within recommended ranges an excessive fluid velocity can be avoided. Thus, leading to a reduction of cavitation.
- In pumps or turbines, avoid sudden changes in speed or flow rates, as rapid changes can result in sudden pressure drops.
- Monitor the Equipment Closely
- Regular inspection of equipment for signs of cavitation-related damage, such as pitting or erosion, can lead to early detection. Thus, preventing more severe damage.